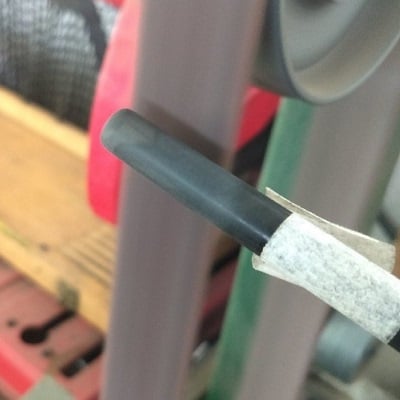
Pros and Cons of sanding a graphite shaft to fit a taper tip hosel
From time to time, I get the question from a clubmaker or hobbyist if it is alright to sand down the tip of a 0.370" parallel tip graphite shaft to fit into a 0.355" taper tip iron or wedge. Before I answer the question and show what the pros and cons are, I first must mention the liability issue. Anything you build or repair, you are liable for what happens. Therefore, it is always the best practice to put in the shaft size that corresponds to the inside hosel diameter.
Why would you need to sand the shaft?
The number 1 reason why clubmakers ask is due to the lack of taper tip graphite iron shaft offerings. Of the models that are available also tend to be on the more expensive side and likely a special order, requiring additional time to fix or retrofit a customer's club.
Why not re-bore the hosel?
This is certainly the solution to using a 0.370" parallel tip shaft into a 0.355" tapered hosel. The problem for many smaller clubmaking shops or for the hobbyist is having the proper equipment to do so. Re-boring requires some sort of drill (drill press preferred) and something to securely hold the head, so the drill bit is parallel to the hosel bore. These fixtures are called ironhead boring devices. High quality drill bits and cutting oil to cool the bits are also encouraged.
How is a taper graphite shaft made?
All 0.355" taper tip graphite shafts start out as a 0.370" parallel tip graphite shaft. One of the last steps prior to painting and applying the polyurethane is to put the shaft into what resembles an electric pencil sharpener to form the taper for the first 2" of the shaft's tip. This devise allows for the shaft tip to be symmetrical and uniformly prepared to the correct dimensions. So, there is a way to safely sand down the tip of a 0.370" parallel tip graphite to fit into a 0.355" taper tip iron or wedge. In contrast, steel shafts are tapered by swaging or reshaping the tip by pressure or force as the wall thickness of steel iron shafts are too thin to sand down.
Can a clubmaker do this by hand?
This is the million-dollar question. Clubmakers do not have access to the same equipment as the shaft makers so the question is whether they can sand the shaft tip uniformly and to the right dimensions without taking too much off and potentially causing the shaft to break after hitting several shots? If they can, how long will it take to complete one shaft? Remember, if you have a whole set to do and it takes 10 minutes to do one shaft, you have over an hour's worth of work to do.
Here are the dimensions of what the shaft tip will look like for the first 2 inches of the shaft. As you can see, the rate of taper is very low (approximately 0.2°). These dimensions do not take in any account the room for epoxy which is generally a couple thousandths of an inch or if you have a name brand iron that has a sloppy or oversized bore. Therefore, test fitting and constant measuring will be crucial if you decide to tackle this endeavor. Also be caution about sanding too far up the shaft because you must calculate the insertion depth of the hosel and probably ½ the length of the ferrule. I recommend putting a piece of masking tape around the shaft, so you know where to stop sanding.
You will have to sand more at the tip than toward the masking tape to create your taper and you will have to make sure to rotate the shaft in the vise if doing so by hand. If using a belt sander, I would recommend a graphite shaft sanding belt rather than a normal sanding belt as not to take too much material as fast. Hand sanding can be accomplished by using a 1" wide strip of medium grit sandpaper and use a shoeshine method to evenly sand around the shaft tip.
Limitations to look for
Parallel tip graphite shafts come in all sorts of weights and geometric configurations at the tip. The lighter the shaft, the thinner the walls will be. Granted, the tip section is not as thin as other areas due to the stresses at impact. This is what a normal graphite shaft will look like. For a 0.370" shaft (outlined in white) will have an opening in the tip to allow air to escape. If the opening is 0.200", this allows for only 0.085" of material on each side of the shaft.
The yellow dotted line represents the 0.355" dimension. As you can see, it is not that much material that is taken off. The further up the first 2" of the shaft tip, there is even less material that is removed.
Next is a diagram of a low balance point or tip heavy graphite shaft. The opening in this case is only 0.134", which allows for 0.118" of material per each side of the shaft. In this case, it would be much easier to sand material from the tip.
The skinny
The internet is full opinions and how to videos regarding trying to make a 0.370" shaft fit into a 0.355" tapered hosel. My best advice is to find a shaft that matches the hosel diameter. If you can't, the next solution is re-boring the hosel (whether you do it or take it elsewhere to have it done professionally). The last resort would be to carefully - and I mean carefully - sand the shaft, constantly measuring and test fitting to make sure you do not take more than necessary to affect the integrity of the shaft. If you take too much off and the graphite shaft breaks, then not only is the manufacturer not going to warranty the shaft, but you could also end up hurting someone or damaging property.